Automotive
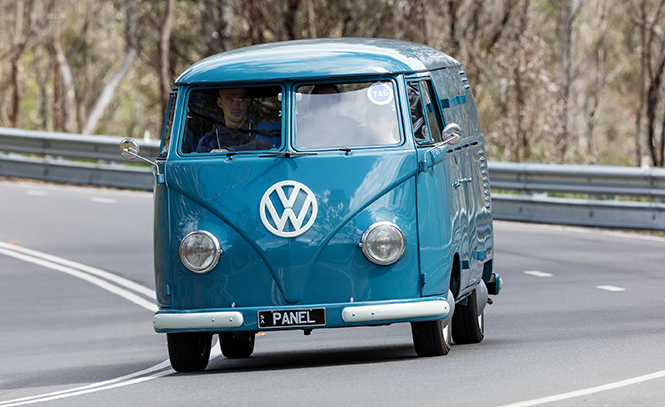
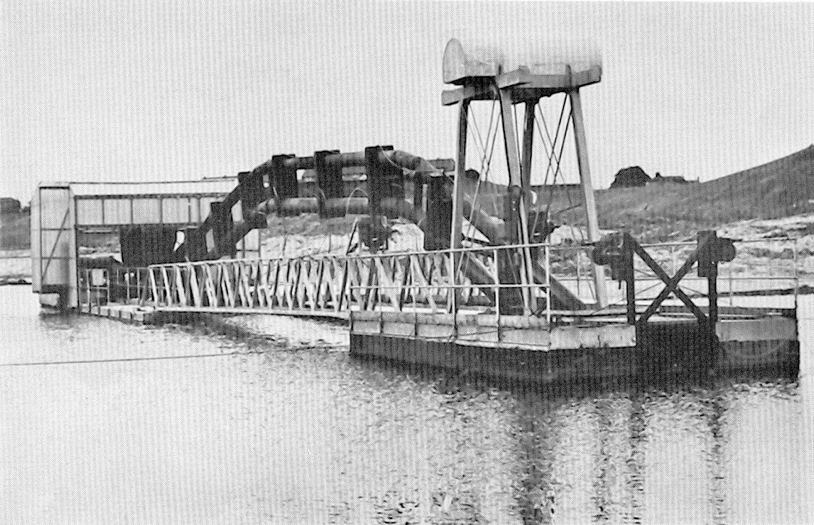
The zinc spraying of a new Jet Pump Dredger provides an interesting example of the very widespread use of metal spraying. The dredger extracts sand by high-pressure suction jet, and has an output of 250 tons of sand per hour.
The vital statistics of the dredger are length 41M (135ft), width 6.7M (22ft), and height from the water line to the top of the hoist 4.55M (15ft). Fabricated in mild steel the dredger will spend its entire working life afloat on the quarry lake, so that the problem of corrosion is quite considerable. The contractor gritblasted the steelwork and sprayed with zinc. Below the water line a deposit of 100µm (0.004”) zinc has been applied followed by two coats of bitumastic paint; above the water line the dredger hull and deck structure have been gritblasted and zinc sprayed to a thickness of 100µm (0.004”).
In addition to the normal corrosive attack of water, the method of operation creates corrosive and abrasive conditions above the water line so that the best available anti-corrosive treatment is essential. It is anticipated that the metal sprayed zinc will protect the dredger throughout its entire operational life without further treatment.
This case study is courtesy of Metallisation.
The polystyrene props were first cut to shape and then metal sprayed with zinc and steel to strengthen them and make them less prone to dents during movement around the set. Metallisation customer and founder of The CNC Factory Ltd, Ed Hladio, has been contracted to create columns, walls and a 3D topographical map for a recent film.
Ed says: “When I work with film sets I regularly have to repair and patch up props due to damage caused while they are moved around, or through contact with actors and filming equipment. For many months now I have been experimenting with metal spraying on all sorts of surfaces, including apples and wood. So, when it came to creating the new film sets it made perfect sense to me to metal spray the polystyrene shapes to give them strength and protection.”
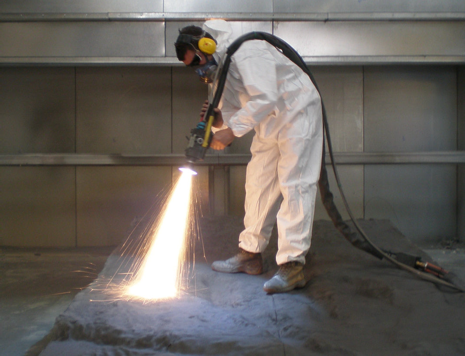