Versatile
No Size Limitation
No Steel Restrictions
Applied in Field
Single Application System but Tough Results
No Drying Time
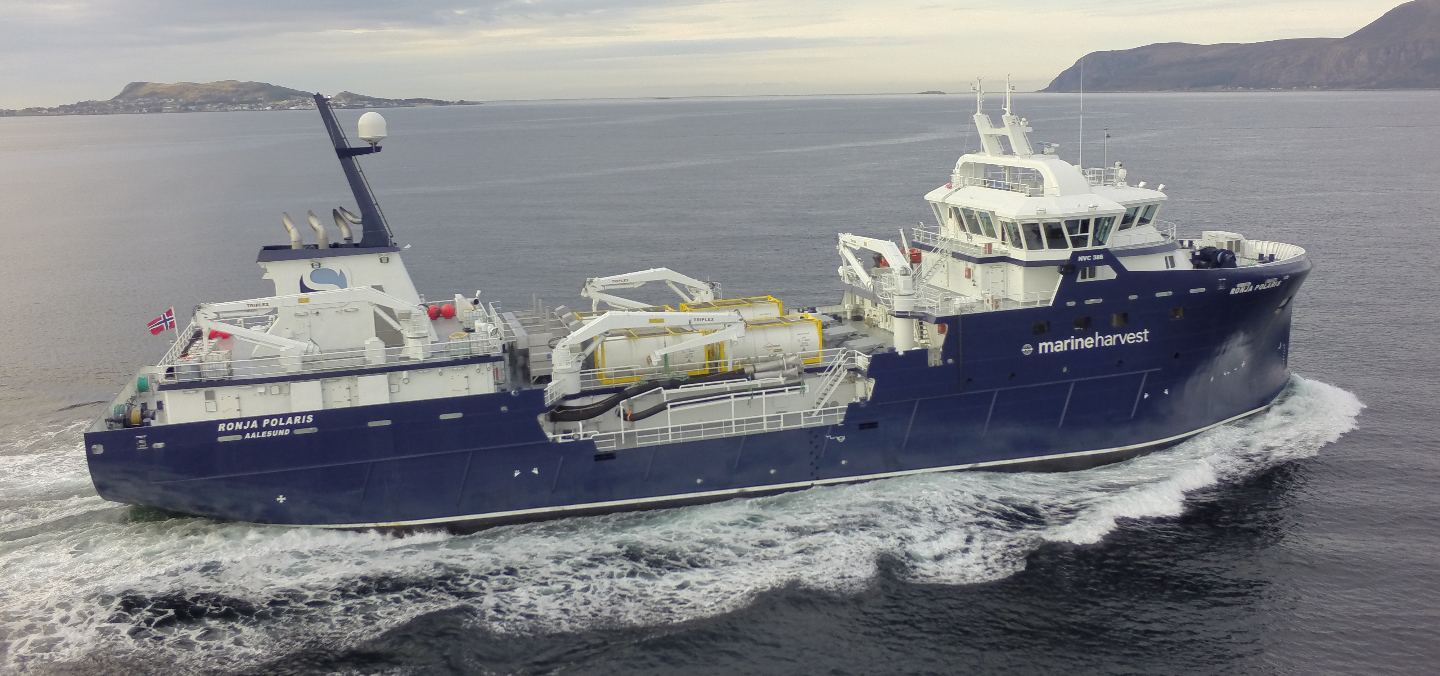
Life Expectancy of Thermal Sprayed Zinc
There are hundreds of case histories relating to the longevity of zinc thermal sprayed coatings on steel. Bridge structures, interiors of potable water tanks, pipelines, and dam locks show, in many cases, over 30 years of service without major repair.
Life Cycle Costs
Initial Costs
In severe environments, applying paint systems over thermal sprayed coatings – while adding to the initial cost – has been shown to create a synergistic effect, extending the life of both coatings beyond their expected lifetimes.
Maintenance Costs
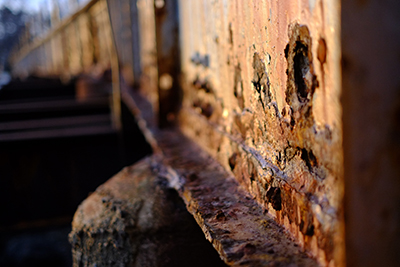
CorrWind Lifecycle Cost Program
IZA has developed the cost model CorrWind to calculate life cycle costs for different corrosion protection systems, such as thermal sprayed Zn, organic coatings and duplex systems of paint supplied over thermal-sprayed zinc. The software is Excel-based. The CorrWind software allows users to determine the sensitivity of total corrosion protection system costs over the expected lifetime of a wind energy structure to input factors, such as the initial cost of the corrosion protection system, expected maintenance costs, rate of inflation over the expected surface life of the structure, financial discount rate and the relationship of initial and maintenance costs to the cost per KWh of the wind energy-generating unit, including the capacity factor of typical wind power units. CorrWind should provide the wind industry with an advisory tool for cutting costs and provide users a way of seeing how the life cycle costs are derived. It is also expected that the model will help provide data for developing corrosion-protection standards tailor-made for the wind energy industry.