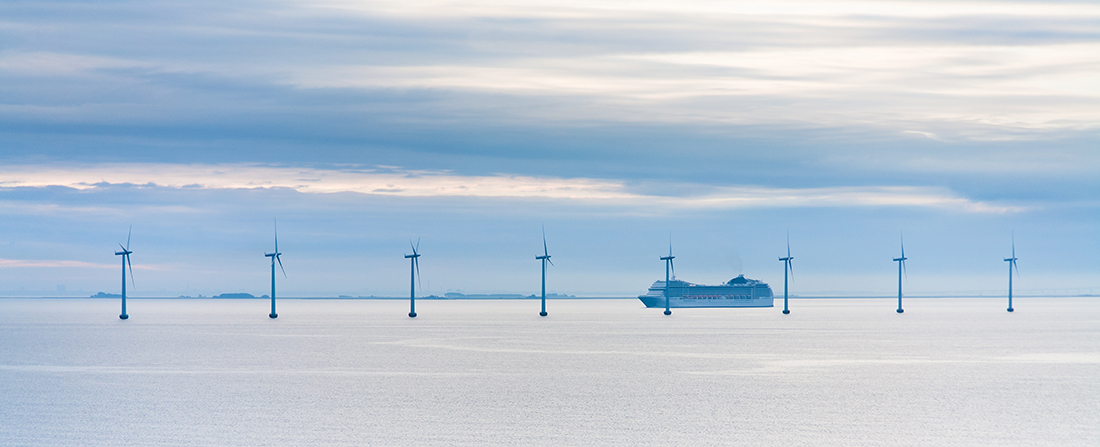
Wind Energy
The International Energy Agency (IEA) 2020 report on the cost of generating electricity states that renewable energy generation, by solar or wind, is now the least expensive source of electricity globally. The financial viability of all energy projects is impacted by current and future market prices, financing costs, site selection, construction delays, equipment reliability and operating costs. For offshore wind, operating costs play a significant role as maintenance costs can be 100 times the cost of onshore maintenance. Thermal spray zinc duplex coatings have a long history of providing corrosion protection for offshore wind turbine towers.
The exceptional performance of duplex coatings for protecting offshore wind towers from corrosion has been validated on the first two windfarms installed in the North Sea that are now decommissioned. The Vindeby farm and the Thunoe Knob farm used duplex coatings on the towers and have met the 25-year design life with no corrosion of the towers.
The Vindeby wind farm was the first multiple tower offshore wind energy installation. Eleven turbines of 450 KW each were installed off the coast of Denmark in 1991. Each tower was protected with a duplex coating consisting of a 120um base of thermal spray Zn-15Al alloy, followed by two coats of epoxy paint of 100um each with a 50um thick polyurethane topcoat, for a total coating thickness of 370um.
After achieving its 25-year design life, the windfarm was decommissioned in 2017. All of the towers were in pristine condition after 25 years at sea. Inspections of the towers as they were brought to shore revealed that none showed any signs of corrosion or even red rust staining. Figure 1 shows the aspect of one of the decommissioned towers. There is no rust evident even at the weld seams.
Figure 1. Vindeby wind farm tower showing no signs of corrosion after 25 years at sea.
(Photo courtesy of Hempel)
The ten 500 KW turbines of the Thunoe Knob wind farm, also in Denmark, were installed in 1995 and were decommissioned in 2020, again after 25 years of service. The coating specification for the Thunoe Knob wind farm called for 80um of thermal sprayed zinc with 2x100um of epoxy paint and 50um polyurethane top-coat for a total coating thickness of 330um. The towers were inspected in 2014 after 19 years at sea and revealed that the galvanized steel landing dock and stairs, and the duplex thermal sprayed zinc coatings on the towers were in excellent condition, again with no red rust or red rust staining.
During inspection, the shackles that anchor the lifelines fastened around the towers were observed to have caused some damage to the paint system. Wind and wave action lift the lifelines, causing the shackles to impact the tower and damage the paint. Also, the shackle movement scrapes the paint off the lifeline mounting brackets. However, although the paint has been removed from the mounting bracket and in areas of impact on the tower, the zinc remains in place providing sacrificial protection, and no corrosion is observed.
Figure 2 shows one of the towers. In Figure 2a) there is no sign of corrosion at the welds or access door. The hot-dip galvanized landing dock is also corrosion free. In Figure 2b) no corrosion is observed on the lifeline brackets even though the paint has been removed from the mounting bracket and in areas of impact on the tower. The duplex coatings on the Thunoe Knob wind towers easily met the 25-year design life with no maintenance.
3a) Tower base and landing dock 3b) Lifeline bracket
Figure 3. Thunoe Knob wind farm tower.
Based in Chepstow, Wales, Mabey Bridge has extensive experience in the production of wind turbine towers, with a specialist factory designed to produce up to 150 towers per year. The company manufactures wind towers from flat sheet to final fit out at its Chepstow factory. The whole process from rolling, welding, coating and fitting out a tower takes around seven to ten days.
Wind turbine towers are exposed to harsh external environments, particularly those in an offshore location. Mabey Bridge is well-established in the wind energy market, serving several major manufacturers and increasing the number of UK-made components in wind energy installations.
The metal spraying process used is a typical specification for this type of structure. The surface of the wind towers is prepared by blasting with a mix of GH25 and GH40 steel grit using a 12.5mm nozzle at nine bar pressure. The areas to be sprayed with zinc are grit blasted to standard SA3.
The blasted sections are then transferred on the blast rotators to the metal spray booth. The zinc coating cures instantly so the tower sections can be rotated directly on the outside diameter. For a land based turbine, various areas are zinc coated with typically 60-120 microns of zinc, The metal sprayed zinc coating is applied to areas more susceptible to corrosion due to assembly damage and normal usage. Specifically, these areas include the studs, brackets, internal fixing areas, the connection flanges located at both ends, plus 300mm internally and externally from the flanged ends. The base section of the tower has an access door, where the internal and external surfaces of the tower are zinc metal sprayed to the top of the access hatch plus 300mm.
After metal spraying is complete, the tower sections are transferred to dedicated paint spray booths. A typical paint specification would now see all areas of the tower section, except the flanges, being sprayed with around 50 microns dry film thickness (DFT) of a 2-component zinc rich epoxy primer coat. The flanges are left unpainted, as the profile of the metal sprayed zinc aids the strength and friction of the bolted joints. There is an approximate curing time of two hours at 40 to 50 degrees Celsius. The mid-coat, commonly a 2-component high build epoxy, is then sprayed at around 120 microns DFT for the internal surfaces of the tower and 150 microns on the external surfaces.
There is a further two hours curing time required at 40 to 50 degrees Celsius. The final top coat to be applied is around 50 microns DFT of 2-component gloss acrylic polyurethane to the external surfaces of the tower. There is approximately four hours curing time required at this stage, again at 40 to 50 degrees Celsius. This specification of zinc metal spray and paint is quite typical for land based wind towers.
This case study is courtesy of Metallisation.
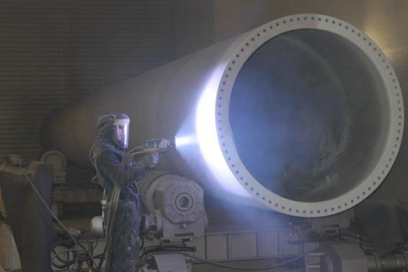
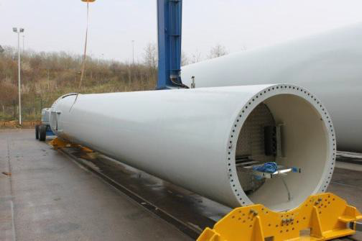